In this article, we summarize the main differences between designing industrial plants compared to civil ones. Their distinct characteristics, functionalities, and purposes, along with the larger scale and higher power requirements typical of industrial installations, call for a different design approach.
These differences necessitate the use of specialized design software for each type of project, as well as different construction and maintenance methods. One example is the level of detail for components: unlike architectural design, industrial designers typically know the specifications of necessary components from the start.
Before diving into the specific differences between these two types of systems and the required functionalities for their design software, let’s first define what is meant by “plant design.”
What is Meant by Plant Design
The general term “plant design” refers to the engineering sector responsible for the design, construction, and installation of all types of systems, whether hydraulic, electrical, or ventilation-related. Covering a broad range of disciplines and applications—from building construction to industrial plants, and auxiliary machinery systems—the specific needs of each sector can vary significantly.
In this article, we will focus on a specific part of mechanical plant design dedicated to the treatment and transportation of fluids. Within this context, we will examine two areas of application (civil and industrial), which, despite having some similarities, differ significantly in both purpose and execution. We will explore the different challenges posed by these two design types, which require distinct methodologies and software tools.
If we were to summarize the main differences between a civil plant and an industrial one, we could say that civil plants are essentially auxiliary to buildings, managing sanitary water, heating, and gas distribution. In contrast, industrial plants are dedicated to the transformation or treatment of raw materials, processed through a series of chemical or physical processes.
In the following sections, we will analyze the differences between these two design types and, in particular, the software functionalities required for each.
Mechanical Plant Design in Civil Engineering
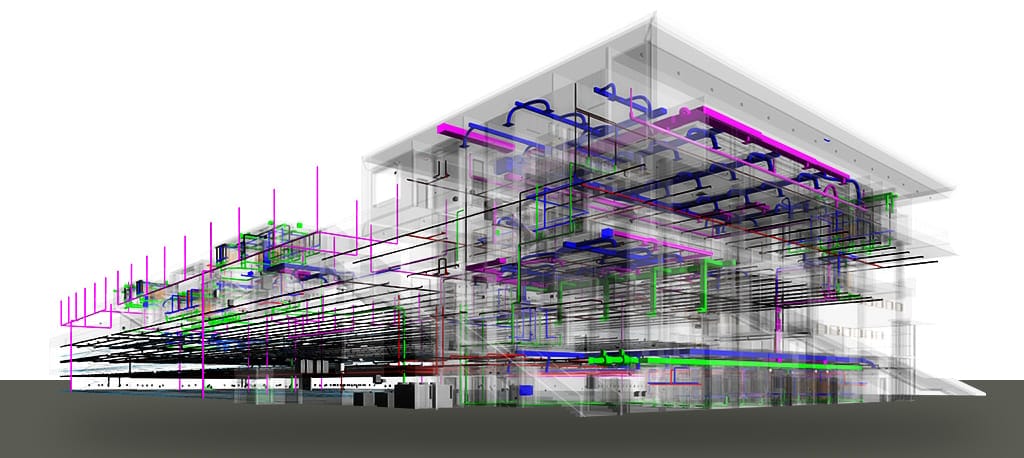
Mechanical plant design in civil engineering involves systems that transport and collect fluids to service buildings—this is why the term “services” is used in English. This category includes systems for the supply of hot and cold sanitary water, wastewater disposal, heating systems, and gas distribution.
What these systems have in common is that they are essentially distribution or collection systems with relatively simple operational requirements. Pressures can range from a minimum of 0.02 bar to 4 bar, and temperatures are generally between -2°C and 70°C (heating systems).
Another feature of civil plants is their structure: they are typically simple, following a tree-like scheme with one or more main risers and as many branches as there are user connections.
Given these characteristics, the functionalities required in civil plant design software become clear:
- A library of sanitary and heating fixtures (e.g., sinks, toilets, radiators).
- A library of pipes and components for plumbing or gas (e.g., elbows, tees, valves, pressure gauges).
- The ability to model the systems in 3D within the building and generate a bill of quantities.
Software for Civil Plant Design
Software used in this field is typically an add-on to architectural design programs, commonly referred to as MEP modules. MEP (Mechanical, Electrical, and Plumbing) defines software tools that allow for the design of all service systems in buildings, particularly: mechanical (ventilation and air conditioning), electrical (lighting and power), and plumbing (water, gas, and heating).
MEP software is BIM-based, allowing management of all systems typically found in buildings. Notably, the term “plumbing” is used in MEP (rather than “piping”) to avoid confusion with industrial plant design.
Another characteristic of these systems is that they are usually built directly on-site by plumbers or electricians, following general instructions provided by the designer or project manager.
A widely used MEP software in Italy is Revit, which, in addition to traditional architectural design commands, has a specialized module (Revit MEP) that allows for easy design of service systems.
Mechanical Plant Design in Industrial Engineering
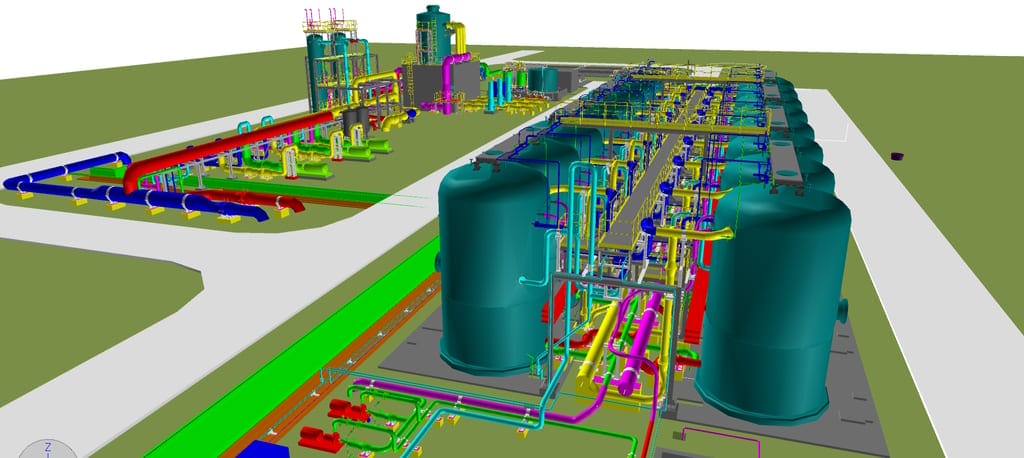
Mechanical plant design in industrial engineering refers to process plants dedicated to transforming or treating raw materials. This category includes plants from various industries, such as:
- Oil & Gas: Production, treatment, and distribution of hydrocarbons like oil and natural gas.
- Basic Chemicals: Production of basic chemicals used as raw materials for a wide range of products, such as plastics, fertilizers, pharmaceuticals, and building materials.
- Paper: Production of paper and related products, such as cardboard and packaging.
- Water Treatment: Facilities for treating and purifying water to remove organic and inorganic contaminants from urban or industrial fluids.
- Food & Beverage: Production of food and beverages, as well as the processing of agricultural and livestock products for retail and large-scale distribution.
- Pharmaceutical: From drug production to packaging and disposal of waste products. Common equipment includes reactors, distillation columns, blenders, and dryers.
- Steel: Production of steel and other products from ferrous minerals. Facilities are usually integrated, covering all stages from raw material processing to the final product.
- Mining: Extraction and processing of raw materials, whether solid, liquid, or gaseous.
- Waste Treatment: From the separation of recyclable materials to volume reduction, biological treatment, and waste incineration.
A common characteristic of many industrial plants is that they sometimes operate under critical pressure and temperature conditions (e.g., -130°C / 1500°C or -10 bar / 60 bar) or handle potentially toxic or hazardous substances.
Another unique aspect of industrial plants is their construction: they are usually prefabricated by specialized companies and assembled on-site by expert fitters and welders.
The complexities involved in this type of design make it necessary to use more advanced software, which, starting from a general process study (P&ID), allows the plant to be designed using only materials compatible with that particular line (piping classes).
Software for Industrial Plant Design
Among the best industrial piping software in Italy is ESApro, which, through a series of specific modules (ESApro P&ID, ESApro 3D Piping, ESApro Isometrics, and ESApro Cable Trays), enables the design of an industrial plant from scratch.
The use of dedicated industrial design software is essential due to the higher complexity of these systems, which involve multiple disciplines. These tools offer a 3D representation of the plant, allowing every component to be detailed: from piping lines and valves to equipment and instrumentation.
The differences in construction methods compared to civil plants further underscore the importance of using dedicated industrial design software. This software allows for the extraction of technical pipe drawings (isometric sketches), providing the fabrication workshop with all the necessary information for prefabrication and assembly.
In conclusion, using software that does not meet the specific needs of industrial plant design is one of the key mistakes to avoid. It is crucial to use piping-specific software when designing an industrial plant, while limiting the use of MEP software to civil systems.
For more details, contact us.
Initially written by Francesco Pais.