Introduction – Your actual piping analysis tool
Five years ago, perhaps ten years ago or perhaps twenty-five years ago, you purchase a piping analysis tool. At this time, you considered it was the best for you on the marketplace…or the only one. A lot of tools have been available since, but do you still have the best for your need or your budget?
This presentation will show you the numerous advantages of PASS/Hydrosystem compared to others on the market.
If you are using your actual tools since years, you surely spent time and money in procedures and training. We surely have solutions for you to save most of your investment.
Reason 1 – Multi-variant Graphical User Interface
Most of the tools are mainly considering schematic representation of the network.
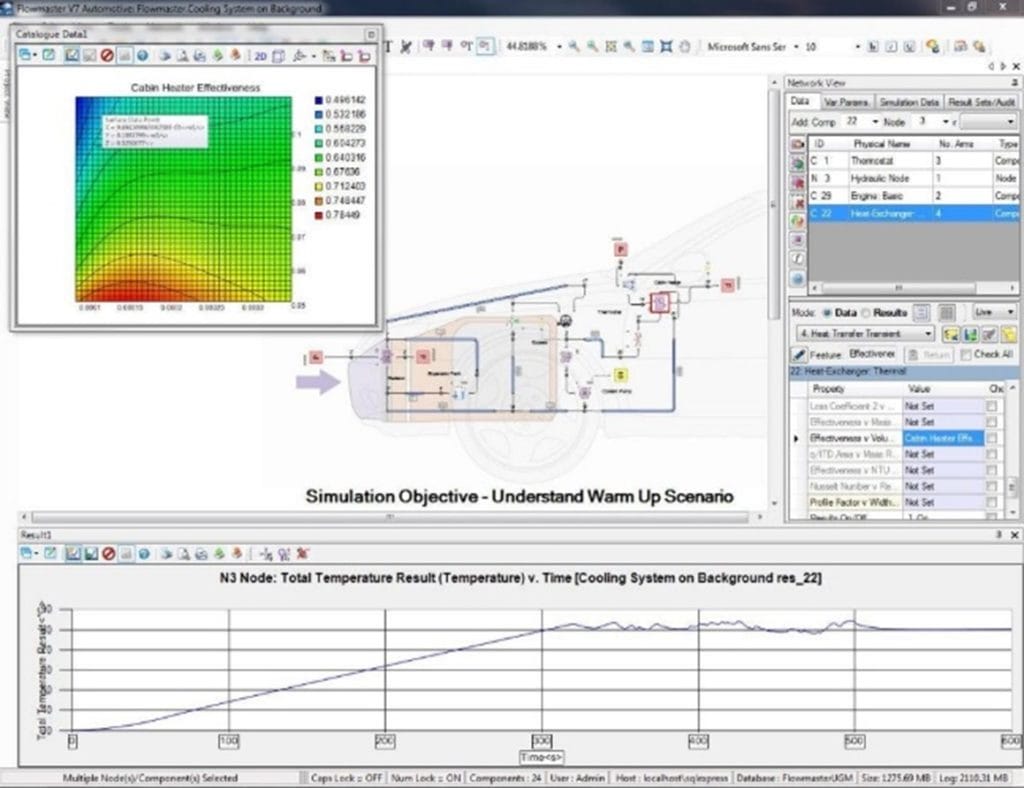
Flowmaster GUI as example 1
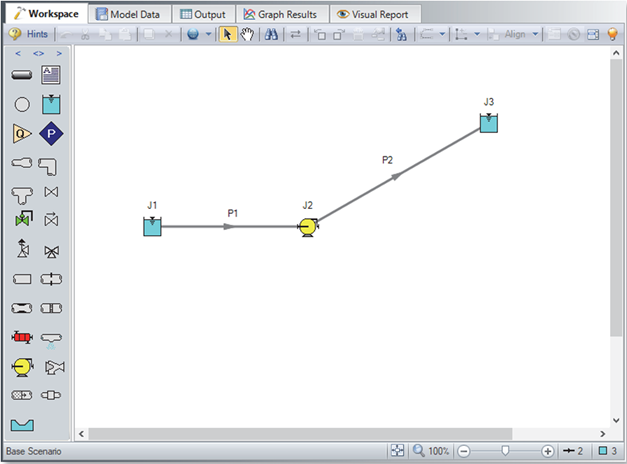
AFT Fathom Schematic GUI as example 2
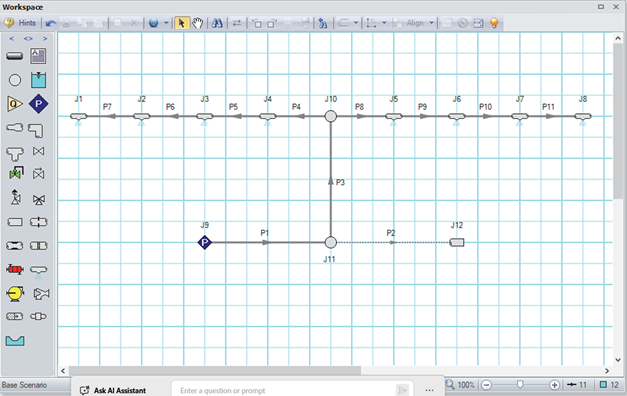
AFT Fathom Isometric Pipe Drawing Mode as example 3
Hydrosystem can work with a large spectrum of pipeline types on different stages of design and offers unique multi-variant graphical representations of the model.
The program can switch between different modes and levels of detail (PFD/P&ID – like unscaled scheme with regulated level of detailing, 2D scaled distributed networks on background map, and single line or solid 3D scaled, or unscaled representation for process piping) depending on what is suitable for a specific design phase and pipeline type.
Hydrosystem allows flexible copy/paste features, including the whole fragments. Scenario manager with variables and formulas helps to quickly change input data for different modes of operation of analyzed pipeline.
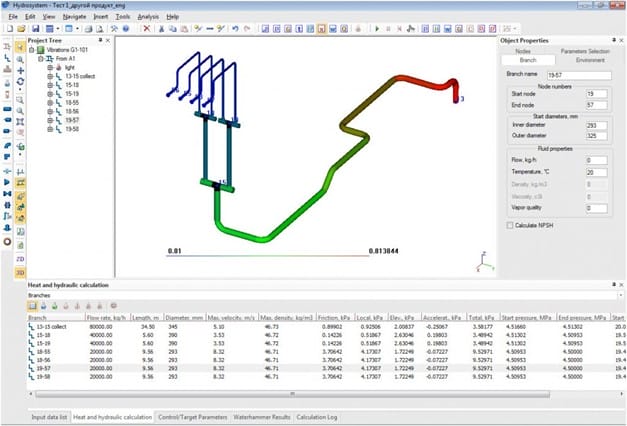
Hydrosystem GUI
Reason 2 – Based on several reference books
On which book is based your software?
Flowmaster, for example, is based on the world-recognized technical book “Internal Flow Systems” by D.S. Miller (Technical Director of British Hydromechanics Research Association).
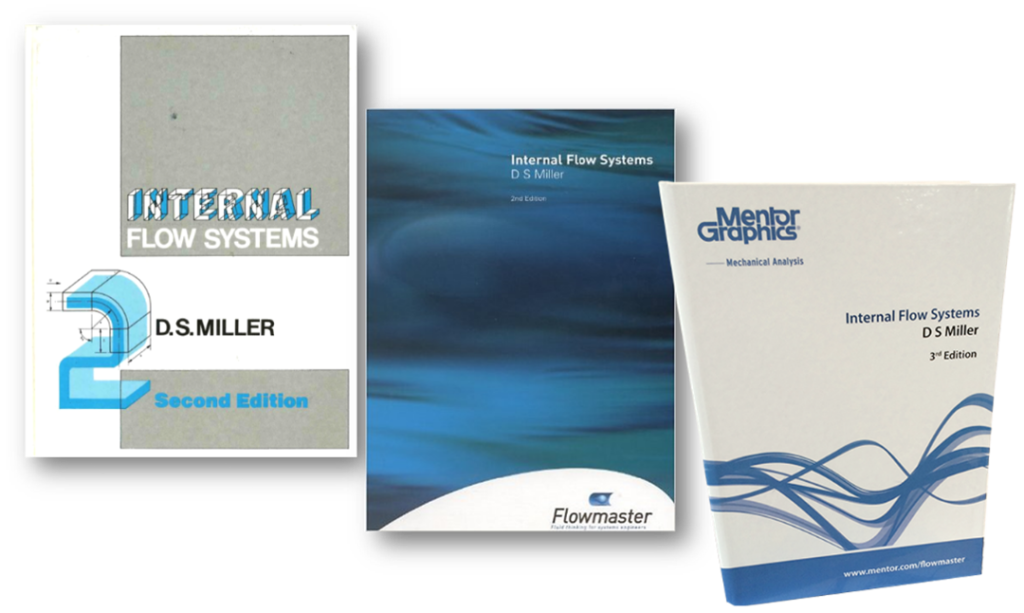
Blessed with world-known piping hydraulic guru I.E Idelchik (“Handbook of Hydraulic Resistance”), Hydrosystem has since evolved into one of most powerful piping flow analysis tools.
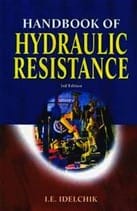
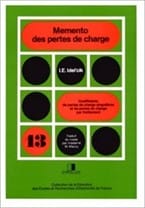
But losses correlations from D.S. Miller and Ito are also included.
Reason 3 – Link with Spaix for pump selection
Hydrosystem delivers a unique opportunity for customers who need to select pumps for their piping systems. The seamless integration with famous Spaix software allows forwarding of all necessary data (duty point data, fluid properties, restriction on NPSH) to Spaix with the push of a button. The user then selects the optimal pump (with all optimization features – impeller trimming, changing the rotation speed, changing blade angle of propeller pumps etc.) and forwards all of the selected pump’s performance curves back to Hydrosystem for final calculation.
Hydrosystem allows the use of Spaix application for pump selection. To use this option, one should input the pump in Hydrosystem as component with known change of pressure equal to the required head of pump and run the pipeline analysis (isothermal or thermohydraulic).
After that “Spaix Pump Selection…” button appears in the parameters window for that component. Pressing that button will call for “Spaix Pumps” application (if it is installed on that PC) for pump selection.
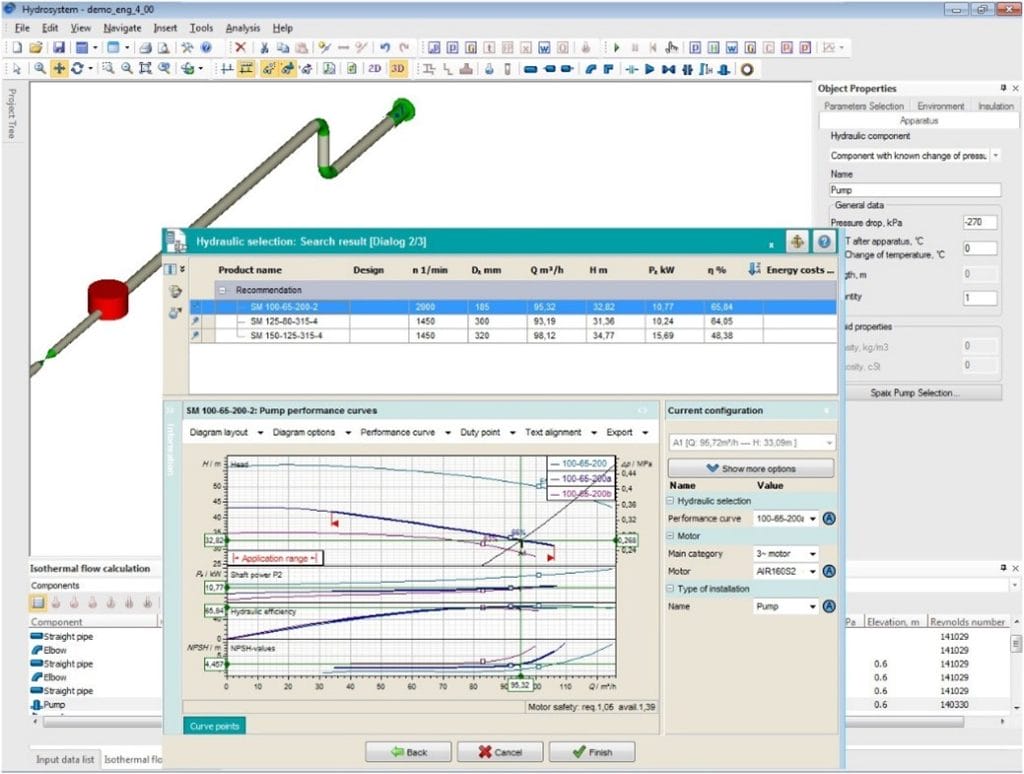
All the necessary data for pump selection (required head of pump, flowrate, fluid properties etc.) are exported into Spaix and users only need to select the pump from the list of pumps compatible with exported data. After pump is selected, all the pump data (head and NPSH curves, pump manufacturer etc.) are imported into Hydrosystem for further analysis and the component with known change of pressure is transformed into pump piping component.
Reason 4 – List and label report generator
Hydrosystem includes a List & Label report generator by Combit for printing input and output data.
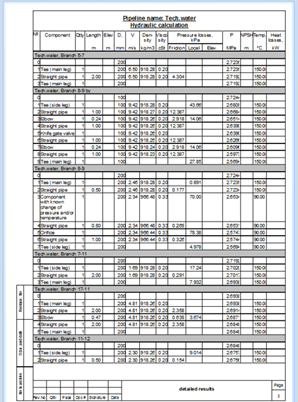
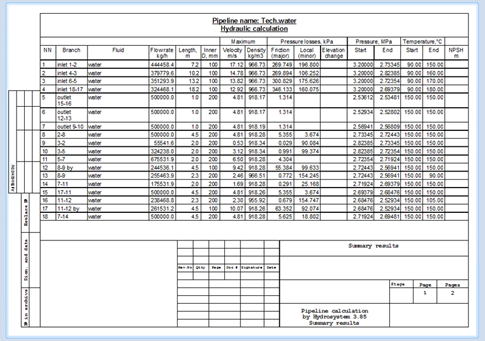
The software allows you to print, preview and save documents (as a List & Label file with an LL extension). The saved files can be viewed and printed using Combit List & Label Viewer, installed with Hydrosystem.
Reports can also be saved in other formats for inclusion in various documents (for example, pdf files for Adobe Acrobat).
The document template can also be changed (for example, editing of the title block format, adding of the company logo, etc.) using the included form editor, List & Label Designer.
Moreover, Hydrosystem software can also generate piping hydraulic isometric drawings.
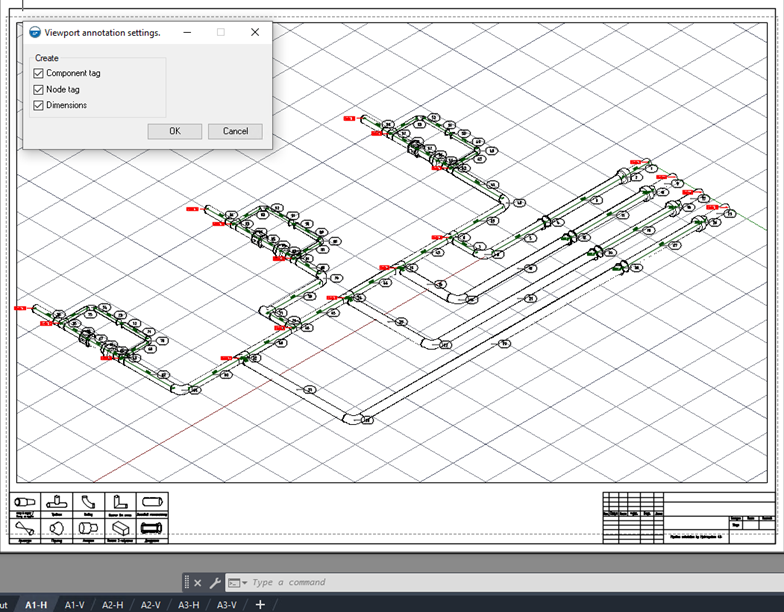
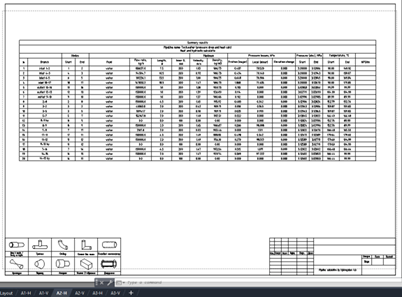
Reason 5 – Easy sizing options
Are you able to size a piping or event to flow balance a branch with your software? Easily?
To size a piping system into Hydrosystem, is very easy as shown in this less than two-minute video
You just need to set the pressure at all inlet and outlets points, and the flow rates in all branches, letting the diameters blanc, then run diameters calculation to determine nominal sizes of pipelines branches.
You may decide to select the diameter to provide the required fluids velocity limit, just setting this value as input data (only in the appropriated branch).
If the diameters of part of the pipeline branches are known, you may specify them as input data. In this case, the program will determine the diameters only for the rest of the branches.
Reason 6 – Real multiphase flows
Does your actual tool compute liquid and gas flows? In the same software or do you need to enter your geometric data two times? And what about multiphase flow?
Hydrosystem provides a calculation engine for all necessary fluid properties and phase equilibrium on the base of fluid composition, for a wide spectrum of fluids and applications, namely with the proprietary Properties and STARS, GERG 2008 and WaterSteamPro libraries.
For more advanced fluid properties and phase equilibrium calculations the program can use the Simulis Thermodynamics library by ProSim.
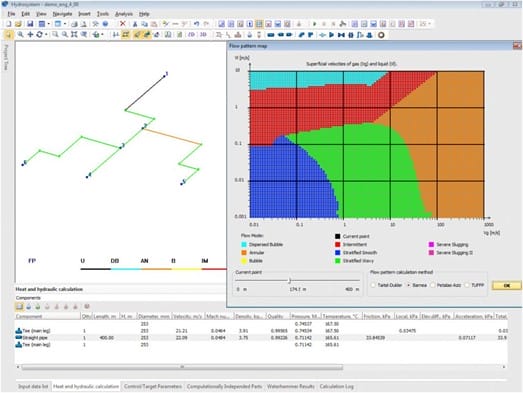
Two-phase gas-liquid flow can be analyzed ignoring mass transfer between phases (so-called “frozen” flow) or considering vaporization and condensation. Frozen flow analysis can be performed both for isothermal flow and as a heat and hydraulic calculation.
Gas-liquid flow is steady, and phases are in the state of thermodynamic equilibrium and having the same temperature and pressure. “Slippage” of liquid and gas phases can be considered, i.e., their movement at different flow velocity.
During hydraulic analysis of a two-phase gas-liquid flow, the pattern of two-phase flow at different points along the pipeline is found, and for all components the following values are calculated: two-phase flow pattern, void fraction and true phase velocities, as well as hydrostatic losses in components due to elevation change, pressure loss due to friction, pressure loss due to local resistance, pressure loss due to acceleration of flow and Mach number.
Several methodologies
Hydrosystem utilizes several methodologies for different calculations, from which the user can select the most appropriate methods for any given task. There is also a high degree of flexibility in which methodologies should be used for various types of components in different situations, which can be set using special rules of method selection for two-phase analysis. User defined rules may be used as well as one of the predefined rules included in the software.
Analysis of two-phase flow considering mass transfer (boiling/condensation) may be performed for pipelines of various structures without recycles. Individual branches are analyzed using direct calculation method, long pipes are subdivided into parts with slight change of calculated parameters, if necessary.
Change of flow temperature and phase composition for this type of flow is calculated using full energy balance equation. First change of fluid enthalpy is determined, then phase equilibrium based on enthalpy and pressure is calculated and finally fluid temperature and phase composition are obtained.
To analyze flow with mass transfer in unbranched pipeline one may enter pressure in the end node of a branch. In this case the fluid temperature is also interpreted as being entered in the end node. The “upstream” calculation is then performed to obtain initial flow parameters (quality, temperature, pressure).
The analysis determines where in the pipeline the fluid state changes to one phase (liquid or gas). In these points the automatic switch to one-phase methods is performed. Similarly, the reverse transition is recognized (the beginning of boiling up or condensation) with switching to two-phase methods.
For two-phase flow in unbranched pipelines Hydrosystem determines where the choked flow occurs in the pipeline (at the end of straight pipes, at the exit, in reducers and abrupt expansions).
Hydrosystem can also do severe slugging prediction and can calculate settling slurry flow (i.e. liquid + solid particles) including flow pattern prediction.
Reason 7 – Direct integration with CAD and BIM
Does your actual tool have a fully automated function to directly convert piping geometry, bypassing data re-entry errors and compressing the time required for such a conversion from hours to minutes compared to manual ‘measure and re-enter’ approaches.
Is it working without any difficulties?
Hydrosystem has numerous interfaces with design and analysis software (see below table).
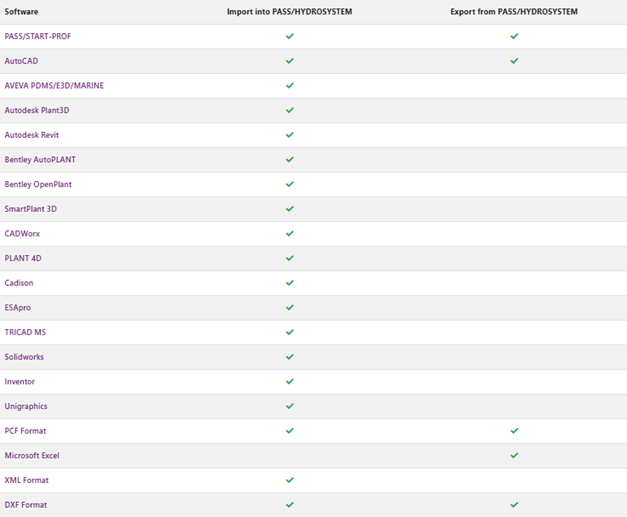
Moreover, the Revit-PASS integration system allows you to accurately transfer the geometry of the pipeline and attributive information from the BIM design system to the system for calculating flow rate, pressure and temperature distribution.
Data exchange is implemented through an open format, which makes it possible to divide the roles of users in the project and optimize the organization’s budget by using only the necessary products.
Using the Revit-PASS integration system and other PASS integration capabilities will allow design organizations to effectively organize the design of industrial facilities due to a significant reduction in the time required for re-entering data. In addition, the use of the integration system when CAD tool and PASS are used together excludes the possibility of errors associated with manual data entry into the calculation model.
Please also notice that import from DXF is smart, i.e. the software recognize pipes, elbows, valves in DXF file geometry, and import them accordingly.
We also have a privileged relationship with our partner ESAin and its CAD system ESApro.
Reason 8 – Direct link to stress analysis tool
Your actual software is probably an accurate tool for water hammer analysis, but has it introduced the ability to automatically calculate and easily export this data as a time history plot to the industry leading pipe stress analysis tools?
You may perhaps export a hydrodynamic force time history plot for use in Intergraph CAESAR II.
Hydrosystem is of course linked to Intergraph CAESAR II but also the other main software from the PASS suite: Start-prof.
Start-Prof provides comprehensive pipe stress, flexibility, stability (buckling), and fatigue strength analysis with related sizing calculations according to international and national codes and standards. First introduced in 1965, it combines a highly efficient solver, powerful analysis features, a user-friendly GUI, an intuitive 3D graphical pre/post-processor, and a detailed help system with embedded intelligence from generations of piping design experts.
It can be used to simulate stress behavior from Hydrosystem results like in the waterhammer example below. Unbalanced waterhammer induced forces on appropriate elements/nodes are calculated and transferred to PASS/START-PROF or other piping stress analysis programs.
Moreover, slug flow parameters (size, frequency, speed of slugs, etc.) for gas-liquid flow can be calculated and reported using TUFFP Unified model. Forces in elbows and flow-turns caused by gas-liquid slug flow are calculated and can be exported to PASS/START-PROF software for accounting them in piping stress analysis.
The PASS/ADD SURGE module implements the classical method of characteristics (MOC), using Riemann invariants and explicit numerical methods. It also considers possible cavitation during transitional flow, considering both, column separation effect and distributed vaporous cavitation.
Reason 9 – probably large difference in pricing
How much money did you invest into your actual tool?
- Did you opt for annual subscription, or did you purchase the software and pay an annual M&S contract?
- Did you really have support and new releases?
- What was your internal investment?
How much did you continue to pay each year for your actual tool?
- Hydrosystem Pressure provides simulation and sizing of any piping network for pressure losses and flow rate distribution related to single phase steady state flow conditions.
- Hydrosystem Pressure&Heat provides simulation and sizing of any piping network for single phase steady state flow and thermal conditions.
- The Multiphase module provides analysis of multi-phase flow in piping systems. The Surge module provides analysis of liquid transient flow in piping systems. The Solid Phase module provides analysis of settling slurry flow.
- Hydrosystem Complete provides comprehensive hydraulic and thermal analysis and related sizing calculations for piping systems of any complexity.
- Minimum Hydrosystem local annual license is starting at 1 000 US$ and the complete perpetual network license price is 12 000 US$
Is Hydrosystem cheaper than your actual tool?
We are at your disposal for a detailed quote based on your needs.
Reason 10 – Worldwide support and highly active permanent development and improvement
Your actual piping analysis tool was probably in the past, one of the leading general purpose 1D computational fluid dynamics (CFD) solutions for the modeling and analysis of fluid mechanics in complex piping systems of any scale.
But what is the situation now?
Your tool was surely acquired by one of the large groups selling simulation tools.
Now part of a large group, the support is depending on the knowledge of the local representative (the former team is probably not present anymore) and the development is decided by the strategy of the group only. No more development or new capabilities for your tool.
First introduced in 1977 and blessed with world-known piping hydraulic guru Idelchik, Hydrosystem has since evolved into one of most powerful piping flow analysis tools.
Founded in 1992, and currently one of leading IT companies, PSRE (Piping System Research & Engineering) Co. now develops Hydrosystem in interaction with leading world expert associations (AIChE DIERS, TUFFP and others). It is part of a complete solution (PASS software) for engineering of Piping Systems and related equipment including engineering consulting.
The program is under highly active permanent development and improvement, with priorities defined by the needs of existing and potential customers.
The worldwide distributors know very well the various capabilities of the software and are listening to customer requests.
The author
Amongst the numerous 1D piping flow analysis tools present on the market, Vincent Soumoy was involved with 3 of them (some since 1994), in Europe and North America, and wrote the following papers.
He worked with Flowmaster from 1994 to 2008 and from 2015 to 2017, with Flownex from 2017 to 2020 and with Hydrosystem since 2019.
He is considering that for most of the requested uses, Hydrosystem is now offering the best quality/price ratio.
Fluids & Co is at your disposal for any question or dedicated quote.
The right 1D – CFD choice for your digital transformation
Vincent Soumoy (Fluids & Co)
CAE Conference – online (2020)
Coupling 1D and 3D CFD Myth or Reality
Vincent Soumoy (Fluids & Co)
NAFEMS – World Congress in Quebec (2019)
Coupling 1D and 3D CFD The Challenges and Rewards of Co-Simulation
David Kelsall (Mentor) & Vincent Soumoy (EURO/CFD)
NAFEMS – Benchmark Magazine (2010) & EnginSoft Newsletter (2011)
Where systems simulation meets CFD
The introduction of 1D models in CFD computations
Vincent Soumoy (EURO/CFD)
NAFEMS – Benchmark Magazine (2009)
Validation des modélisations et flexibilité d’intégration :
deux dimensions incontournables pour les logiciels scientifiques.
Vincent Soumoy (Flowmaster)
Journée Nationale : logiciels pour la modélisation et le calcul scientifique – Paris (2006)
Flexibilité d’intégration et facilité de compréhension : deux nouvelles dimensions pour les logiciels scientifiques
Vincent Soumoy (Flowmaster), Gil Jouhanneau (EDF), Karine Huyge (The Mathworks)
Micad, Paris (2003)
Semt Pielstick successfully apply Flowmaster to ship engine internal and external flows
J.R. Magré, J.L. Bertholom (Semt Pielstick), V. Soumoy (Flowmaster)
Simouest Conference– Virtual Shipbuilding, the current state of affairs, Nantes (2002)
A link between CAD system and simulation tools will help shipbuilders to reduce their delay.
R. de Gongora (Sener), V. Soumoy (Flowmaster)
Simouest Conference– Virtual Shipbuilding, the current state of affairs, Nantes (2002)